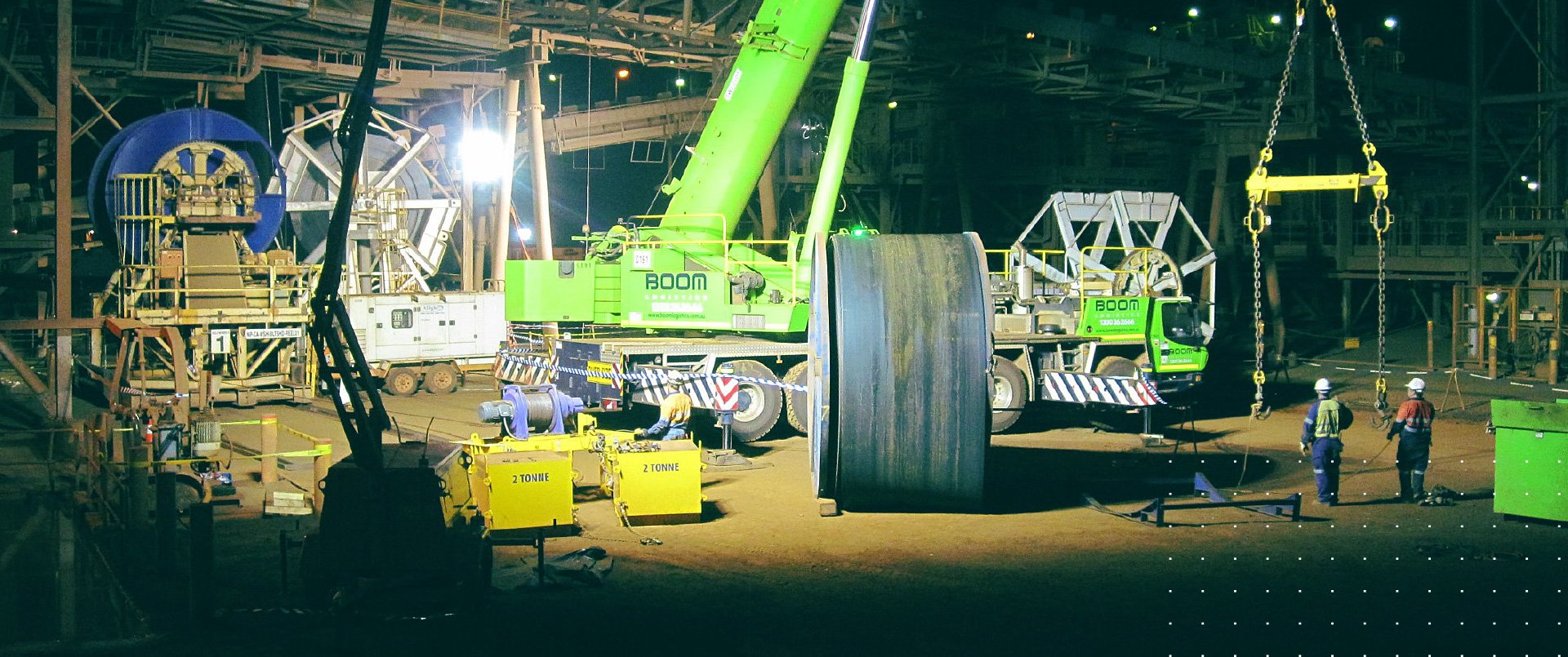
Boosting uptime for BHP Port Hedland
3 MINUTE READ
BHP’s WAIO operations at Port Hedland use hundreds of kilometres of conveyor belts to move iron ore – and every time one of those 160 belts require changing, it forces significant, and costly, shutdowns. Secora was able to cut downtime by 65% and boost contractors’ ‘tool time’ from 38% to over 70%.
THE PROJECT
Secora’s brief was to develop and implement a stable, repeatable belt change process to reduce downtime duration by 30%.
WHO WE’RE WORKING WITH
BHP’s Western Australia Iron Ore (WAIO) division, Port Hedland, WA.
Port Hedland is one of the largest iron ore loading ports in the world and the largest in Australia.
THE CHALLENGE
For Port Hedland’s operations, the most significant portion of the total shutdown budget was claimed by belts.
The duration of belt changes was unpredictable, destabilising shutdown executions and causing cost blow-outs and overruns.
Secora launched ‘Operation Racetrack’ to make belt changeover quicker and more uniform.
We formulated a ‘Lean - Quick Change Over’ approach to mapping, analysing and improving the belt change process. A holistic view was taken starting with scheduling and concluding with the critique and improvement phases.
There were six major steps to executing the project:
Plan and scope the project. Set-up logistics, project management/governance, initiate communications and stakeholder management processes.
Conduct Tool Time studies of contractor work crews to understand current performance and identify key areas of waste and inefficiency.
Train the crews, planners and other stakeholders in Lean QCO methodologies, using simulation models and content which related closely to the tasks they were executing. This changed their perspective on their workplace and tasks, and helped them to see process waste and downtime which they did not see before the training and awareness sessions.
Together with the up-skilled stakeholders, develop and implement robust sub-processes for the key elements maintenance framework. These explained in detail ‘how to’ execute the task, set a consistent quality standard, provided templates for completion, offered mistake-proofing checks and provided a platform for continuous improvement of the sub-process.
Support the implementation & focus on the things that really make a difference and frustrate the stakeholders.
Set up visual management during implementation to drive the operational discipline of hitting deadlines.
Continue regular Tool Time observations in addition to the project work, to monitor effectiveness of framework improvements.
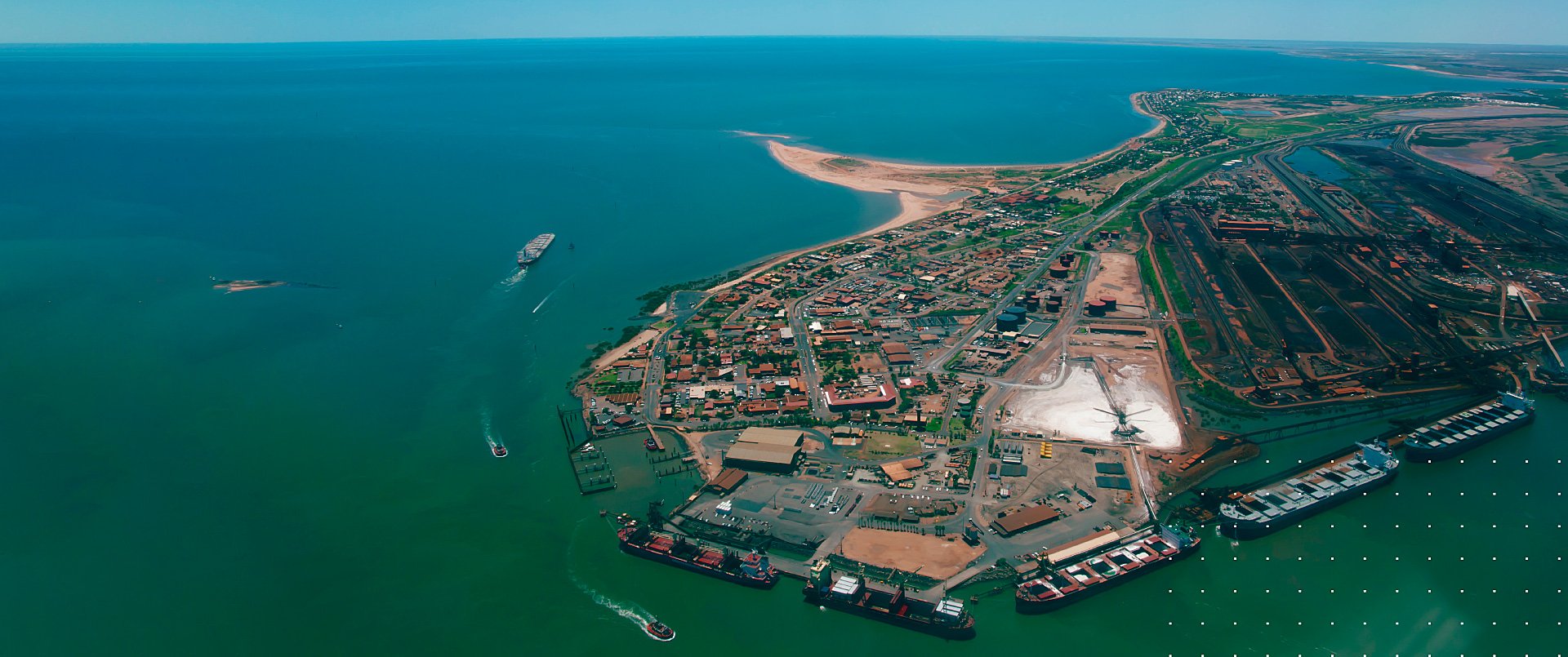
The project yielded over $180 million in additional margin in the first six months after implementation.
THE RESULT
Six months after project completion:
Total realised shutdown hour reduction was greater than 156 hours
Contractor Tool Time was increased from 38% to greater than 70%
Schedule adherence was within +/-10%
Change-out time reductions were 30–65% against baseline values.
12 months after project completion, the same team went on to execute large scale improvement projects including:
Removal of 0.5km of redundant skirts from site conveyors
Scraper maintenance optimisation
AU$3.2million/pa cost reduction in cranes and scaffold usage.