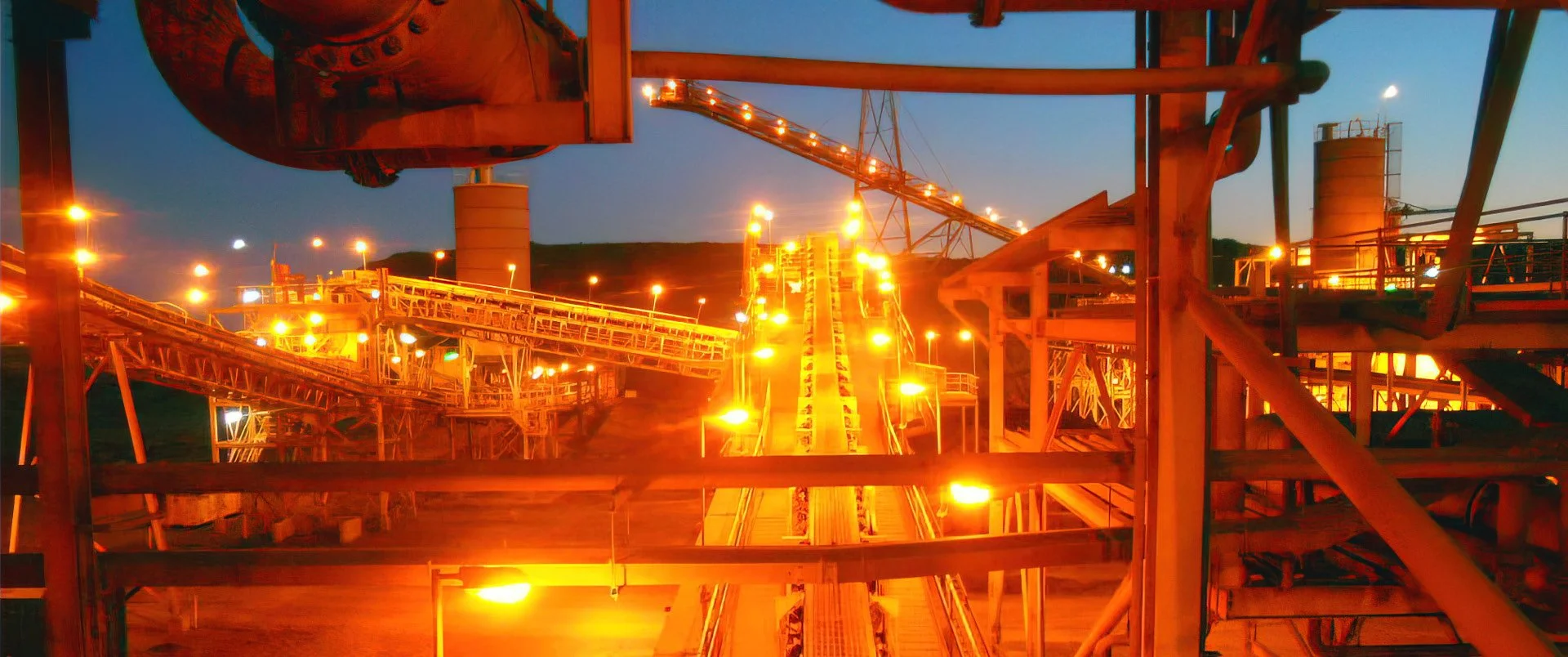
Tightening mine shutdown durations
3 MINUTE READ
Secora helped a mining client reduce planned shutdown duration by 13% and resource usage by 15%, identifying over 170 improvements. A robust shutdown planning process was established, which increased controls, enhanced communication, and ensured continuous improvement – all supporting the mine's expansion plans.
THE CHALLENGE
Secora was engaged to review the Mine Maintenance function and identified opportunities to reduce the duration and improve the productivity of planned shutdowns. This was critical for supporting planned mining expansion without significant capital investment.
WHAT WE DID
Secora applied Quick Change Over (QCO) and Detailed Job Planning (DJP) techniques to:
Identify shutdown drivers and critical path jobs.
Critically examine and challenge tasks with work groups.
Implement and trial refined processes at the next opportunity.
Debrief major jobs, refine processes, and establish new procedures.
Schedule ongoing improvement workshops.
THE RESULTS
The improved Shutdown Management Procedure resulted in:
13% reduction in shutdown duration.
15% reduction in resources (labour and materials).
Specific improvements included:
Streamlined work crew mobilisation, adding 2 hours of tool time per shift.
Improved and prioritised permit issuing process.
120% reduction in plant ramp-down time.
30% reduction in crusher main shaft change-out time.
34% reduction in crusher concave liner replacement time.
A review of the shutdown planning process yielded significant improvements:
Increased controls around work scope and job freeze processes.
Greater emphasis on detailed job scoping, involving stakeholders and third-party service providers.
Enhanced scrutiny of resource requirements through Resource Challenge meetings.
Improved communication with all shutdown stakeholders via a Shutdown Planning Information Centre.
Better monitoring and debriefing of critical path and major jobs, enabling effective planning and ongoing improvements.